Table of Contents
ToggleHydraulic cylinder seals classification
Hydraulic cylinder seals are mainly divided into:
A, static seal
B, dynamic seal
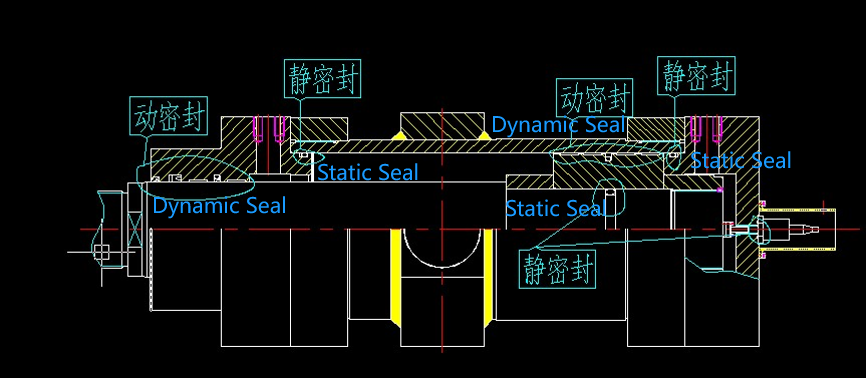
Static seal failure analyses
Static Seals: Seals between relatively stationary bonding surfaces are called static seals.
Classification of static seals:
Static seals are categorized into many types, and the most frequently used in hydraulic cylinder applications is the O-ring. In other words, hydraulic cylinder static seal failure analysis is used primarily for O-ring failure analysis.
The following are the main causes of 0-ring failure in hydraulic cylinder applications.
1.Permanent deformation
As the O-ring seal with synthetic rubber material is viscoelastic, the initial setting of the compression and resilience blocking capacity after a long time will result in permanent deformation, gradual loss, and, ultimately, leakage. This permanent deformation and elasticity disappearance is the main reason for the loss of sealing performance of the O-ring. The following are the main causes of permanent deformation:
- Excessive compression
- Excessive working pressure
- Temperature is too high
- Excessive permanent deformation of material
Preventive measures: Selection of materials with low deformation rate; appropriate groove design, confirmation of hydraulic cylinder working conditions.
2.Extruding
- Sealed parts exist in the geometric accuracy (including roundness, ellipticity, cylindricity, coaxiality, etc.) is poor, between the parts of the different centrifugal and high-pressure expansion of the inner diameter and other phenomena will cause the sealing gap expansion and gap extrusion phenomenon aggravated.
- O-ring hardness on the gap extrusion phenomenon also has a significant impact; the smaller the hardness of the O-ring material, the more serious the O-ring gap extrusion phenomenon is.
- High pressure or high pressure without the use of a retaining ring will cause a gap extrusion phenomenon.
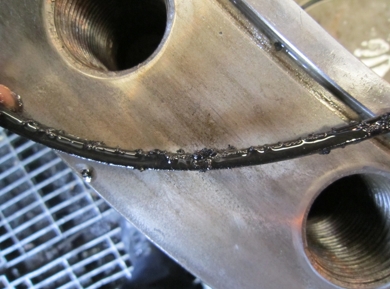
Preventive measures: to ensure the machining accuracy and rigidity of the parts, can improve the hardness of the material, choose the appropriate fit clearance or increase the retaining ring
3.Abrasion
- The roughness of the surface is a direct factor affecting the friction and wear of the O-ring surface. Generally speaking, the more smooth the surface, the less friction and wear, so the sliding surface roughness value is often very low (Ra0.2~0.050μm). However, tests show that the surface roughness is too low (Ra less than 0.050μm) and will cause friction and wear to bring adverse effects, so choose the appropriate surface requirements.
- High temperatures and dusty sealing environment infiltration of dirt seals produce relative motion, or seal surface treatment is not clean enough, which will lead to seal wear and seal failure.

Preventive measures: use recommended groove finishes, use self-lubricating materials, remove wear-causing components and environment.
4.Pre-compression volume
The O-Ring is installed in the groove, and an initial amount of compression should be reserved for its sealing performance. The amount of pre-compression relative to the section diameter W varies for different applications. Typically, it is about 13% to 30% in the case of static seals for hydraulic cylinders.
Preventive measures: Selection of the right amount of pre-compression.
5.Ageing
Temperatures exceeding the expected temperatures or too rapid and frequent temperature changes can lead to cracks and deterioration of the seals.
Preventive measures: Replacement of high-temperature-resistant sealing materials.
6.Softening
The rubber material is not adapted to the sealing medium, resulting in softening of the O-ring.
Preventive measures; selection of materials suitable for the medium.
7.Damage caused by installation
Due to parts chamfering is not suitable, equipment personnel errors or O-ring size selection is not reasonable, the amount of interference is too large, the seal hardness or elasticity being too low, etc., caused by the O-ring being sheared, resulting in seal failure.
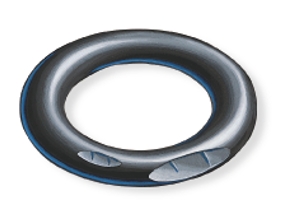
Preventive measures: Remove sharp edges. The design of the grooves should be rationalized. Choose the right size of seals, and choose the seals with higher elasticity and hardness.
Dynamic seal failure analysis
Dynamic seal: the seal between the relative movement of the joint surface is called dynamic sealing.
Classification of dynamic seals:
Dynamic seals, according to the contact form, are divided into contact seals and non-contact seals; in hydraulic cylinder applications, they are mainly contact seals (lip seals, extruded seals, rotary lip seals)
In hydraulic cylinder applications, there are several main cases of dynamic seal failure:
1.Seal squeezed into the gap
Excessive system pressure and overdesigned mating gaps lead to seal extrusion damage.
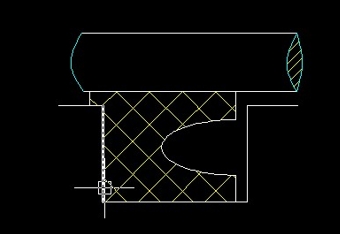
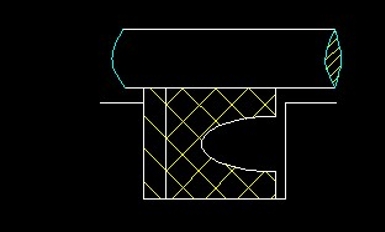
Preventive measures: To prevent the seal from being extruded, it is common to increase the retaining ring, choose a suitable fit gap, or increase the hardness of the material.
2.Damage by foreign impurities
The presence of metal ferrous chips in the hydraulic cylinders due to the assembly not being cleaned by the assemblers resulted in the hydraulic cylinder parts being strained and the seals being damaged.


Preventive measures: thorough inspection before assembly, clean parts, do not allow any impurities into.
3.Selection of unsuitable materials, temperatures, pressures and media
By choosing the wrong material, temperature, pressure and media, the seal will be hardened, aged, softened, etc., which will directly hydraulic seals lead to leakage.
Preventive measures: selection of right materials.
4.Back pressure damage
When seals are installed in pairs, back pressure is generated due to the leakage of trapped oil between the two seals, thus damaging the hyd seals. Installing leakage holes is the usual method of eliminating back pressure on seals.
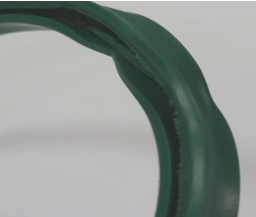
Preventive measures: add a pressure relief hole on the side of the piston head against the lip or use a combination of double-acting seals.
5.Influence of material and surface roughness of mating surfaces
- The surface roughness of the shaft or hydraulic cylinder has a great impact on the sealing performance; its surface roughness Ra should not be greater than 0.32μm, but the surface roughness Ra can not be less than 0.08μm Recommended surface roughness of the mating surface value Ra0.08 ~ Ra0.32μm between.
- The material of the mating surface also affects the life of the O-ring. The greater the hardness of the sliding surface material, the higher the abrasion resistance, and the stronger the ability to maintain a smooth finish, the longer the life of the O-ring. This is also an important reason why the surface of the hydraulic cylinder piston rod is chromium-plated.

6.Damage caused during installation
The ends of holes and shafts that may be touched when installing hydraulic cylinder seals need to be chamfered by 15~20° to prevent the sealing surface from being damaged, resulting in oil leakage from the seals.
7.Abrasive wear
When the gap of the seal has a relative movement, dust and sand particles in the working environment, etc., are adhered to the surface of the piston rod, the dust ring(wiper seals)fails to play a good dust, so with the reciprocating movement of the piston rod with the oil film together with the cylinder, become invasive sealing the surface of the abrasive particles, sealing the wear and tear of the cylinder seals, so that it loses its sealing properties.
Guide element failure analysis
1.Guide tape delamination peeling
a, guide belt fiber reinforced layer bonding may be problematic, as there is not enough adhesive force; the whole lateral piece of peeling does the cylinder work.
b, guide belt self-lubrication is not good, and hydraulic cylinder body friction is too large. The Ambassador of the lateral shear force is too concentrated in the guide belt itself.
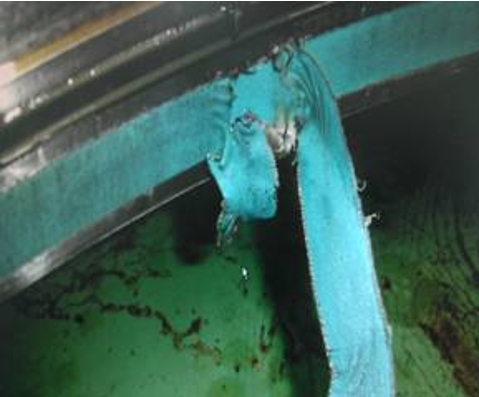
Solution: Use a support belt with a higher support force and good self-lubricating properties.
2.Cracking and edge biting of the guide strips
The side load force of the cylinder reaches the limit of pressure resistance of the guide belt; long-term work under high pressure will lead to rapid aging and failure of the guide belt.
Solution: Use a guide strips with higher pressure capacity or use more guide strips .
3.Guide strips band breakage
The hydraulic cylinder diameter is too small; use the whole roll of bearing strip. Phenolic resin guides, according to different processes, are divided into “ring” and “tape” two kinds; the ring in densification and structural stability are better than the tape, the production cost and versatility of the tape are poor, and the cylinder diameter is too small the internal structure of the material will be easily damaged due to the excessive bending of the guiding belt, leaving hidden dangers.
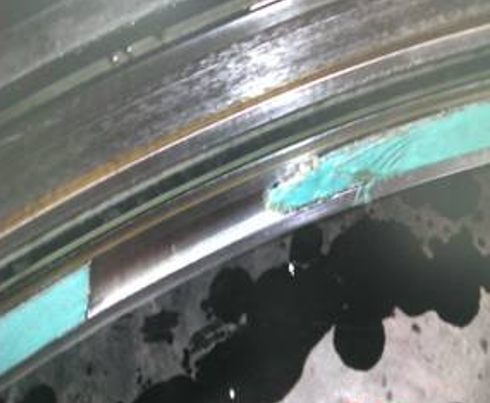
Solution: Generally, when the cylinder diameter is less than Φ100mm, the guide strips cannot be used, and the guide ring should be used instead.
summarize
The causes of hyd cylinder seals failure are summarized in two main points:
1,Seal design error
Design errors are usually caused by the designer’s lack of knowledge of the product, such as the wrong pressure selected for the hydraulic actuator seals, the wrong choice of material, the choice of seal gap and tolerance, and the design of the groove where the seal is placed is not reasonable.
2.Improper use of seals
Good hydraulic actuator seals, if not used properly, can cause the entire product to fail, such as
Wrong installation, too high or too low operating temperature, installation errors, etc.
If you want to evaluate your existing seals for replacement or improvement, TYS Seals is your smart choice, TYS not only provides hydraulic seals but also provides you with suitable sealing solutions to help you quickly find the right seals for your needs, TYS Seals’ extensive stock and long term relationships with top suppliers around the world enable the highest quality seals to be produced at the fastest rate. Contact the TYS team for more hydraulic seals.